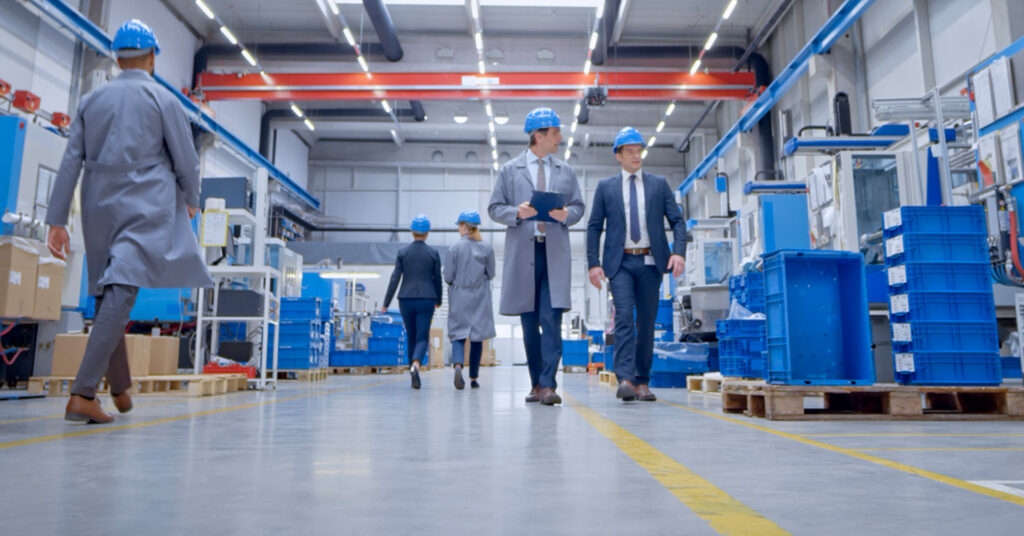
How to Prepare for an OSHA Inspection—Q&A With an Expert
Michael Rubin, a shareholder and OSHA attorney at Ogletree Deakins, shares his expertise on navigating OSHA inspections and how to prepare your company and team for them.
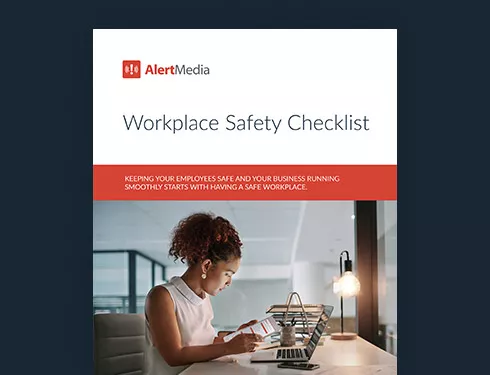
Since the agency was founded in 1971, the Occupational Safety and Health Administration (OSHA) has been performing inspections on workplaces to identify hazards and unsafe conditions to ensure workplace safety. Knowing what to expect when an OSHA compliance officer shows up for an inspection can be a challenge for any organization. With more than 400 pages in OSHA’s Field Operations Manual, companies need expert advice to prepare for an unexpected walkthrough.
Michael Rubin is a shareholder and OSHA attorney at Ogletree Deakins, and he has worked with companies through the inspection process time and again. He sat down with us on The Employee Safety Podcast to discuss how organizations can prepare for an OSHA inspection and how they can prevent any complications or mistakes during the process itself.
You can listen to the episode on Apple Podcasts, Spotify, or below.
Workplace Safety Checklist
Q&A With Michael Rubin, Shareholder and OSHA Attorney at Ogletree Deakins
What are the most common misconceptions you hear from organizations about the OSHA inspection process?
Well, one huge misconception is that you basically don’t have rights. But you have a host of rights, and those rights are actually spelled out by OSHA itself. Then the other thing is that citations are really allegations. So, when companies get a citation, oftentimes they look at it almost as if it’s a formal legal adjudication. But really, it’s a document setting forth allegations. It’s OSHA’s view of the situation; it’s not a neutral judge’s view of the situation. So that ties back again to having rights and a bunch of options if OSHA does show up.
“For any violation, there's generally four things OSHA needs to prove: They would need to show the standard applies, that it was not complied with, that an employee was exposed to the hazard or violation, and, finally, that the employer knew about the violation or hazard or should have known about it.”Michael Rubin Shareholder and OSHA attorney at Ogletree Deakins
How do you recommend organizations prepare for an inspection?
Well, there’s some reference documents you can look at if you really wanted to be a student of the OSHA inspection process. There’s something called the OSHA Field Operations Manual. There’s one chapter that talks about inspections, and we’ve actually used what’s written in that manual on site when we think an inspector might be going the wrong way with something, we’ll just remind them that, yes, it is our right not to have a manager sign a statement. It is our right for any employee not to speak with OSHA if they don’t have a subpoena. These basic rights are either expressly or impliedly set out in this field operations manual.
If OSHA does show up and you’re not prepared and you don’t know what to do, at minimum can you say, “Hey, we need to pause this until I can get my legal representation on site,” or do you not have that right? Do you have to let them do what they want to do?
This is a fantastic question. So, if OSHA shows up without a warrant, what you could do is really one of two things: Number one—you could say, “We’re inclined to consent, but we need our attorney to get here.” And in the Field Operations Manual, it does instruct OSHA inspectors that they should accommodate such requests and wait up to one hour. We had one matter in New York where I told the OSHA inspector we needed to wait because the safety director was coming to the site. I was already on site and the OSHA inspector said, “Well, we don’t follow the Field Operations Manual. We only wait 15 minutes.” I said, “Okay, well, you know, we could just not consent. And in a way, you’ll be waiting until the safety director gets here because you don’t have any right to start the inspection until we consent.” So, you could go either route. You could ask, as a courtesy, for the OSHA inspector to wait. If they say, no, we’re not waiting. You would say, well, we can’t consent to the inspection because someone who’s indispensable to the process can’t be here right now. Sometimes, they get frustrated with that. But ultimately, every OSHA inspector understands that is a hard and fast rule that, number one, companies have to consent. And number two, if they want to delay the inspection, they can. So, there’s actually pros and cons of working it out, but you can use the consent that OSHA needs as leverage for getting some things that you want.
Generally speaking, who could expect to see OSHA knocking at their door? Is it just bigger companies? Could it be a very small organization? Are there particular industries that need to be more worried about this than others?
I’ve heard it said that at least half of all OSHA inspections are of construction companies and construction sites. Construction is very dangerous. You’ve got people working on structures that aren’t completed. You’re working at heights with fall hazards. All of those things. And then with other industries—manufacturing, hospitality, some retail chains—if they have blocked exits, that’s like OSHA low-hanging fruit. Those are the types of companies that OSHA usually is going after or, at a minimum, inspecting.
Who is involved in OSHA inspections?
Besides the OSHA compliance officer, here is who would be part of the inspection process:
Area director — Can accompany the OSHA inspector on the walkthrough and document their own findings
Employee representatives — May be asked questions during the employee interview stage
Employer representative — May be present during the inspection as a legal representative
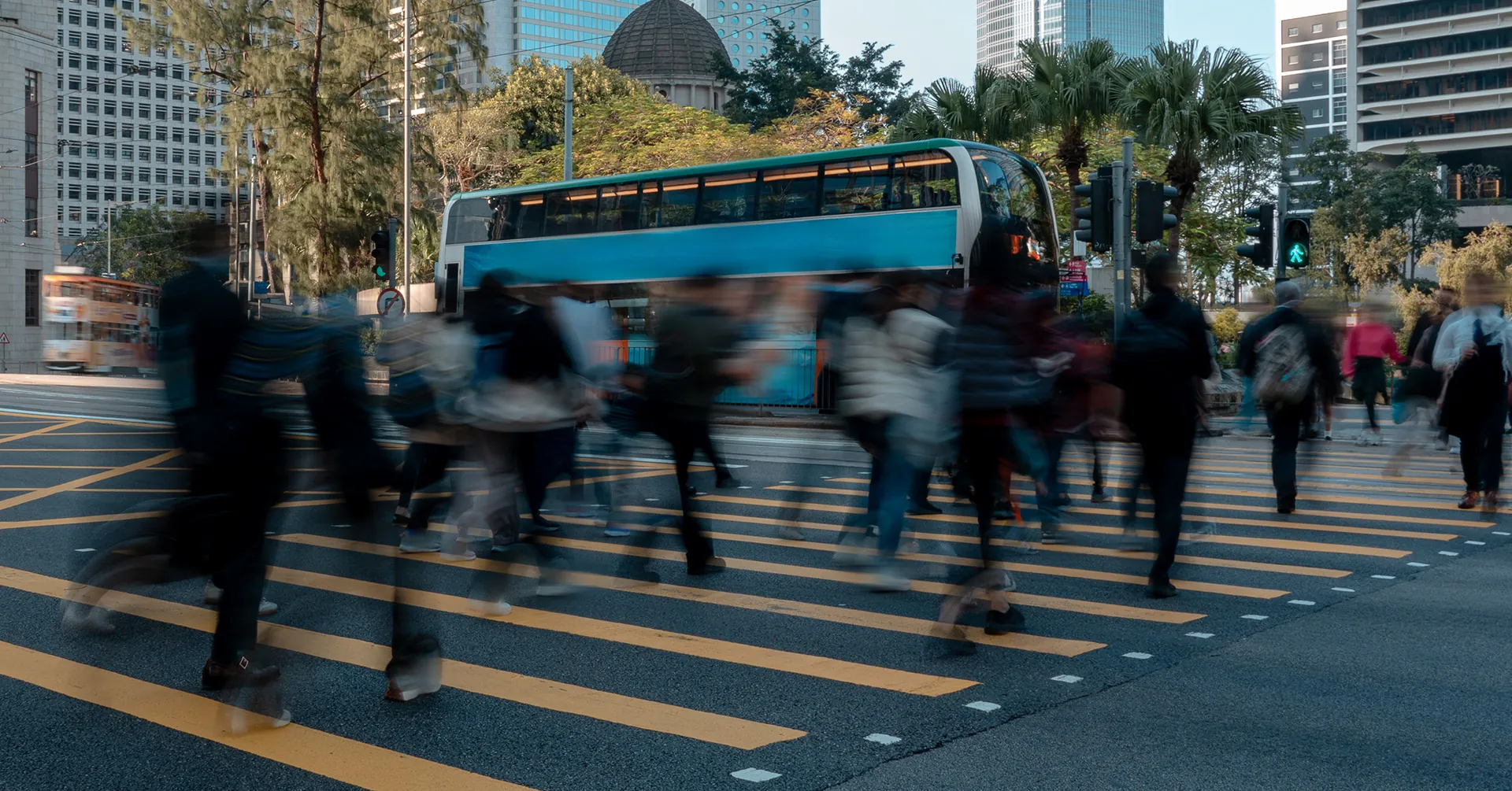
What should organizations do on the day of an inspection?
When the OSHA inspector walks in the door, there’s an opening conference. That’s where you discuss why the inspector’s there and what the inspector plans to do, and that’s when you would go through the whole consent issue. You would say, “We’re inclined to consent to this inspection even though you do not have a search warrant and we know the Fourth Amendment applies.” Once you start saying this stuff, the inspector is going to think, “Okay, I need to be really sharp on this one.” Then you say, “We want to have a protocol, so we know what we’re agreeing to.” And then the inspection would start.
If you do consent, they do have a right to do what’s called the walkthrough, They walk around, and they can take photos. You have the right to take side by side photos, the same photos the inspector takes. They’re generally entitled to speak with non-supervisory employees alone. But employees don’t have to speak to inspectors. It’s voluntary. So, if an inspector shows up at a site, they don’t have a search warrant and they don’t have any subpoenas, you could say, “I’m exercising my right to decline to speak to you.” You do not have to speak to the inspector, but that might be a fleeting avoidance of the employee interview process because they’ll just go get a subpoena. And if you disagree, you’ve got to resort to the legal process. Sometimes, it’s just better to talk.
Another critical thing to mention is managers have a right to have an attorney present with them when inspectors interview them, and they have a right to be prepared. So, if the inspector shows up without a warrant and without a subpoena, which invariably is the case, we would highly recommend you don’t set your managers down for an interview with the OSHA inspector that day. They might give basic information like, yes, this is our workplace, we do this type of work, basic information—but not a full-fledged interview. We would say we’re not doing that today and we’ll schedule it. And we want to prepare witnesses, so they know the reason for the questions, they know what everything involves. And then ultimately, they’re a lot more comfortable with the process.
What are some of the other common pitfalls you should avoid during an inspection?
Making admissions. Oftentimes, companies feel like if they’re brutally honest, it’s going to help them. They think they have nothing to hide and they’re overly deferential because they’re scared. So, you’re just overly cooperative in one sense. And if an OSHA inspector points something out during the walk around, for example, he or she might say these employees need hard hats. You wouldn’t say, “You’re right. We’re sorry, we’ll get right on that,” because number one, the OSHA inspector might be wrong. When OSHA issues a citation, those are allegations. There might be no overhead hazard. There might be no potential hazards to the eyes. What you would do in that instance is you might go over to the employee, tell them to put their hard hat on and leave it at that. So, whatever the inspector says is wrong, you address it, but you don’t make an admission.
I guess if I had to summarize it, I would say, nonchalantly navigating the inspection process is the biggest mistake. When OSHA shows up, they are there to issue a citation to you. Remember, inspectors need probable cause to show up. So, there’s either been reported injury, there’s been an anonymous complaint and inspectors are there following that probable cause, and they’re probably expecting to cite you.
Another pitfall is remembering that everything you say to OSHA is evidence. It can be used in a civil matter. Maybe the OSHA matter gets resolved, and then lo and behold, there’s personal injury lawsuits. One of the first things the plaintiff’s attorneys will do is get that OSHA file. We’ve seen this happen multiple times. When you’re getting interviewed, the questions can be leading. They can be confusing. Sometimes OSHA knows exactly what they need and want to win a case, and they’re going to ask the question that way and you’re going to give a response and not know it’s not exactly accurate. And then it’s embedded in the case, and you’re just stuck.
It seems to me like an OSHA visit is almost like a deposition and as lawyers always say, you can’t win your case through the deposition, but you can certainly lose it.
Well, that’s a very good point you need to know in advance. And that’s why we prepare witnesses for interviews with OSHA inspectors because for any violation, there’s generally four things OSHA needs to prove: They would need to show the standard applies, that it was not complied with, that an employee was exposed to the hazard or the violation, and, finally, that the employer knew about the violation or hazard or should have known about it.
When OSHA inspectors ask questions, they’re going to ask questions about employer knowledge of the hazard, and they might ask how close you were to this, when the last time you looked over there was—and the manager might say, “I don’t know. I felt like I was looking over every minute,” but that might be a wrong answer. And all of a sudden, you just admitted that you had an actual knowledge or at least, at a minimum, constructive knowledge, so you should have known about it after all. You said you were looking over every minute, well, every minute to you might be once an hour. So, you just have to be very careful and understand why these questions are being asked so you can be extremely precise in how you answer.
Two reasons for OSHA inspections
An OSHA compliance officer might show up for one of two reasons. The first might be a requested inspection, where your organization reaches out for an inspection in good faith to discover any ways that you can better follow OSHA standards and improve working conditions.
The second case might be an unannounced inspection where OSHA inspectors show up without warning. This might be triggered by an employee complaint, reported OSHA violations, or an official inspection warrant. During these inspections, the OSHA officer may issue citations for things such as missing/incorrect personal protective equipment (PPE), unaddressed safety standards, or high-hazard situations.
Do you recommend that these organizations do some kind of practice ahead of time, like mock OSHA inspections?
They say, if you want to hit a baseball, it’s probably not a good idea to go to the library and start reading about it. You need to step up to the plate and start swinging and seeing how you do. We do mock OSHA inspections on occasion. They’re really invaluable because they put you on the spot. When you’re in that situation and someone shows up and you might have to tell someone who works for the government “No, we don’t consent,” obviously, that person might not be enthusiastic about that, right? So, just making yourself comfortable doing the mock inspection is invaluable.
Another thing it drives home is the basics. That’s what a mock OSHA inspection is good for. It’s going to hit maybe 10 to 15 items that would come up in any inspection and you’ll have choices on how to react.
What are some of the other very specific things people can do in that mock inspection that will really help them shine? If this happens?
If I show up to do this mock inspection, I would want someone to ask me when I’m the inspector, what’s the probable cause for this inspection? Meaning, why are you here? What’s the legal justification for you looking through our worksite?
Two other big aspects are interviews and document requests. The inspector is going to ask for documents. But what we council is you should not start giving documents without having someone, either management or outside attorney, look at the documents and make sure it relates to the scope of the inspection. So, practice why is OSHA there, where they go, what documents can they get, and how soon can you give the documents? And then practice interviews. OSHA will show up. They want to speak to people right away because there is an element of surprise. OSHA is not allowed to tell you they’re showing up under the OSHA act of 1970 that actually provides for criminal penalties for giving advanced notice. But those are the big things that you would have to go through all of this and go through it for the most part sequentially.
What do you think companies get wrong most often when it comes to safety?
I think the companies that we’ve seen struggle have a fundamental misunderstanding about what safety is. Safety has to be an everyday thing. So really, when it comes to safety and OSHA compliance, training is where it all starts and ends. I think that’s most important: You’ve got to train your workers. You need to have a diverse safety training program. And you’ve got to have a knowledgeable, skilled team and hold everyone accountable.